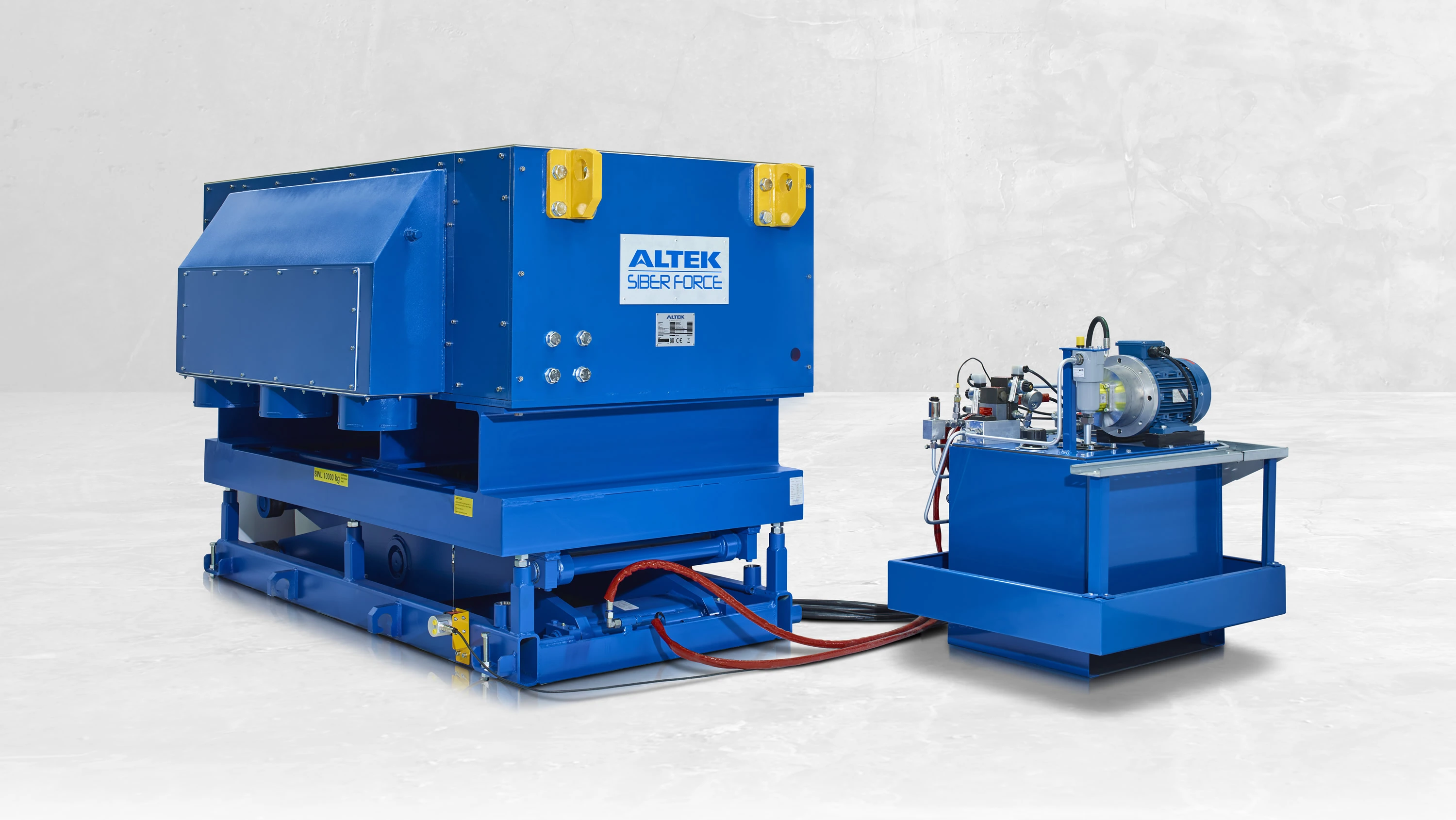
Cost Effective Air Cooled Electromagnetic Furnace Stirring System
The ALTEK inductor is 100% air-cooled and does not require an expensive, complicated and potentially unsafe water-cooling system close to the furnace. ALTEK engineers design, build and install each machine bespoke to individual customer requirements, ensuring a quick and easy transition to the technology. With close to 100 references worldwide, ALTEK have become the preferred supplier of electromagnetic stirrers for many companies due to the unrivalled success and performance each installation has achieved.
Concept
ALTEK’s EMS is based on the principal of a linear induction motor. A low frequency air-cooled inductor is placed on the bottom or side of a furnace. When electrical power is applied to the coil, a magnetic field is generated creating a strong movement of molten metal. The magnetic field penetrates any kind of refractory type or thickness meaning ALTEK can install the EMS on almost any type or configuration of furnace. No physical contact is made with the melt and the system comprises of no moving parts.
Versatile
Altek's EMS is extremely powerful, and can be used in many stirring applications: bottom-mounted, side-mounted, for side-well chamber pumping, multi-chamber circulation and more.
A combination of the specially patented control system and inductor design allow our customers to vary the strength and direction of the electromagnetic field many times during a furnace cycle. This means the stirring effect is optimised whether at a melting stage, alloying stage or holding stage for either bottom mounted or side mounted applications. All these factors mean electrical energy consumption is kept as low as possible whilst also maximising melt rates and alloy yield.
Results
Increased productivity - Increased thermal transfer of burner energy to solid metal, improved alloy dissolution and reduced dross formation all contribute to a significant increase in productivity.
Energy savings - Air-cooled inductor design typically uses 90 -140kWh per furnace cycle, however it also reduces gas consumption by as much as 15%. This equates to large energy savings year on year.
Temperature and chemical homogeneity - Once the stirring cycle is initiated, the thermal gradient between the top and bottom of bath will be ±5°C within 5 minutes.
- Increases furnace productivity up to 25%*
- Reduces energy consumption up to 15%*
- Reduces melt loss up to 25%*
- Rapid chemical and temperature homogeneity
- Air-cooled inductor
- Very reliable – no moving parts and easy to maintain
- Increased productivity
- Energy savings
- Temperature and chemical homogeneity
- Cost-effective air-cooled
- Side mounted EMS
- Bottom mounted EMS
- * depending upon furnace and operation
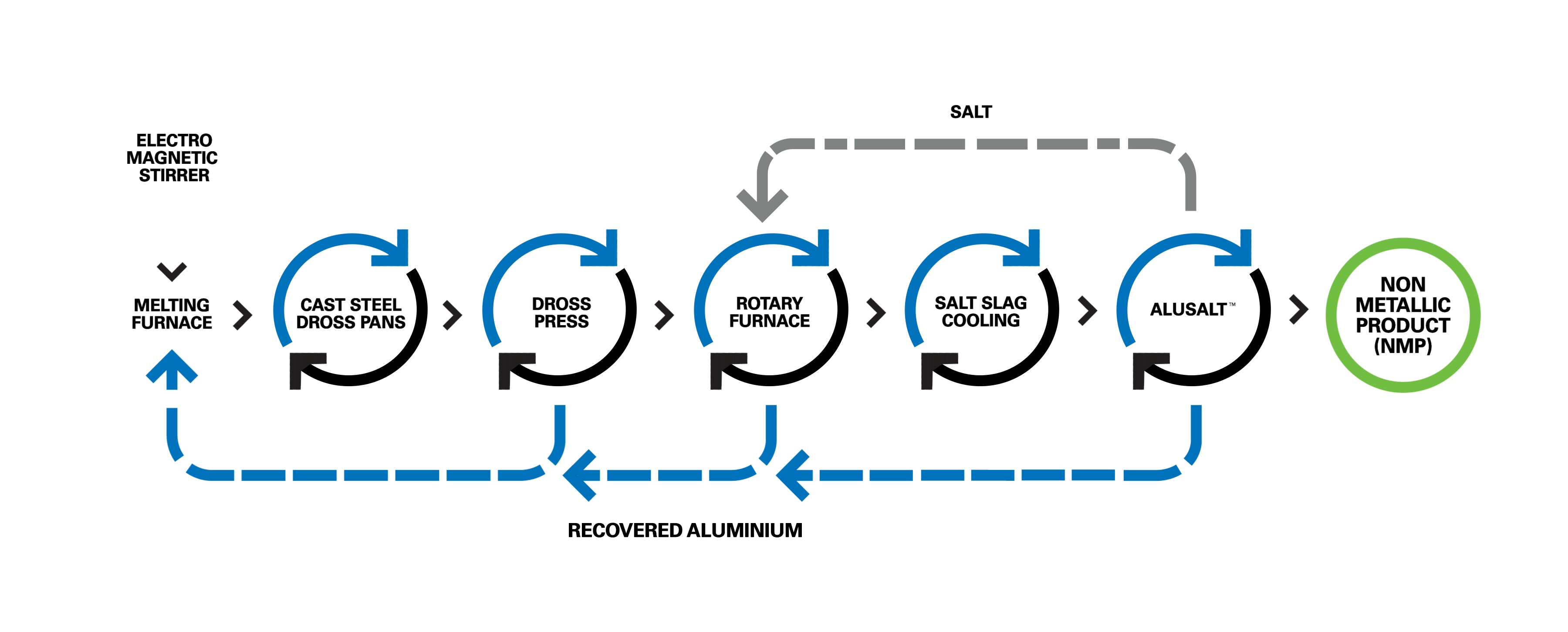
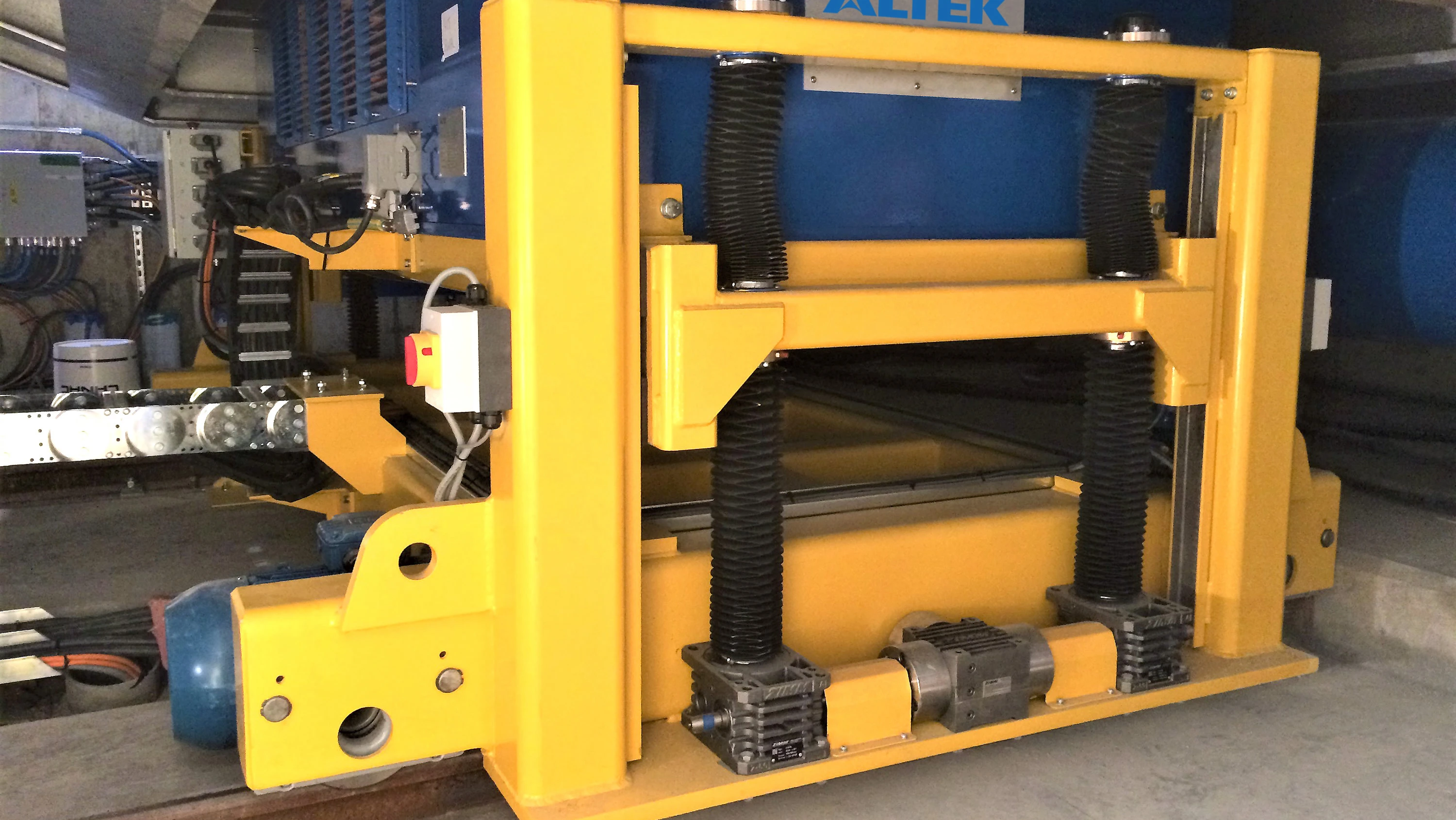
Explore new and exciting possibilities with ALTEK
Fill out the form and our sales team will reach out to start a conversation about how ALTEK can help your business save money.
For urgent enquiries, email us at altsales@harsco.com