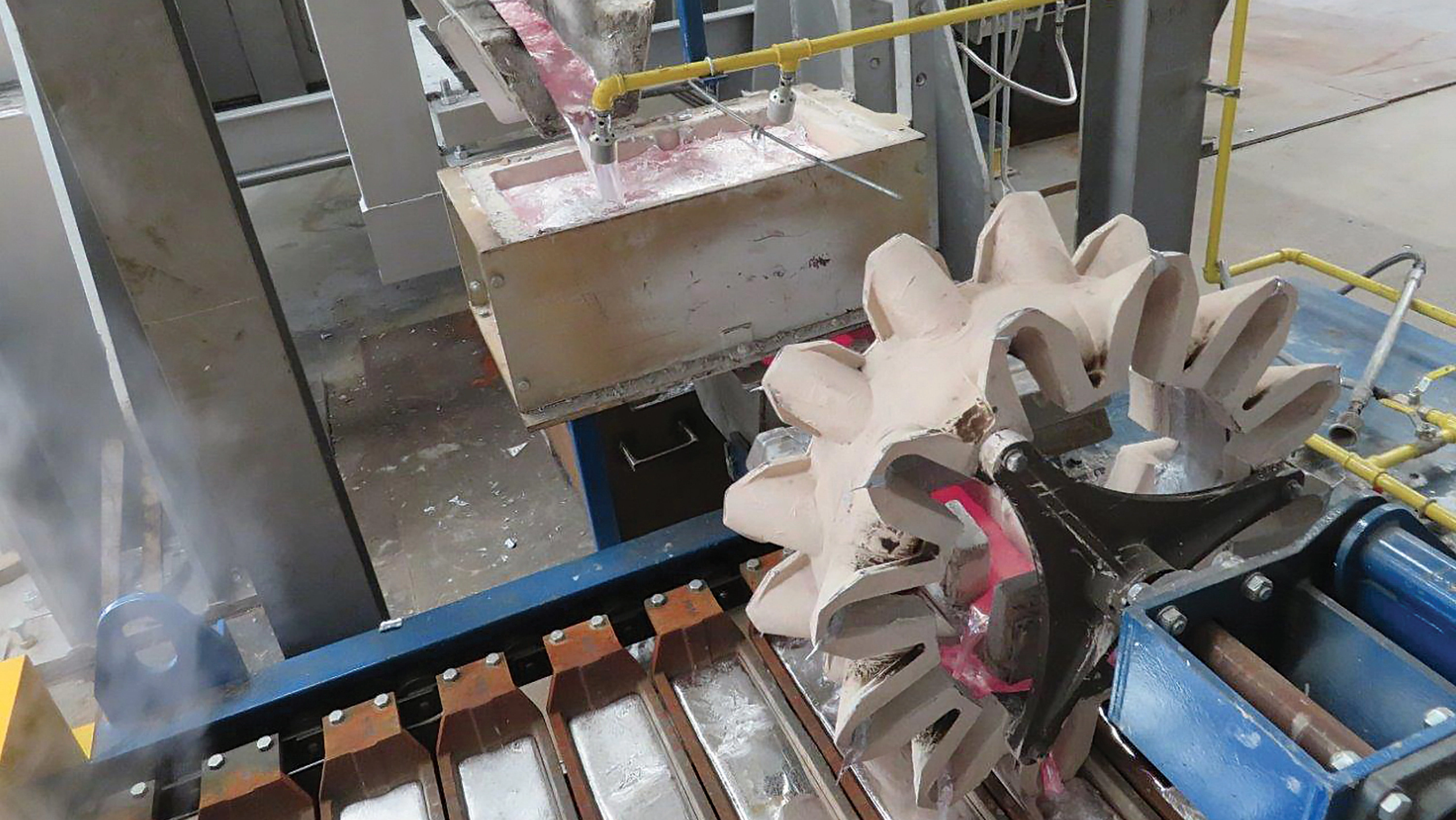
ALTEK Ingot Casting Lines Used To Convert Liquid Aluminium Into Small Ingot Stacks
Ingot casting lines are used to convert liquid aluminium, typically from Tilt Rotary Furnaces or Holding Furnaces into small ingot stacks. Altek’s ingot casting lines come in a variety of sizes depending on the size of ingot mould required, throughput requirements, and preferred cooling methods, and are manufactured to high standards of precision with the best materials available to give a machine requiring a minimum of maintenance and extended component life.
The Ingot Caster
Liquid metal is poured from the furnace into our “star wheel” caster. This pours the metal into the ingot moulds with minimal turbulence and great accuracy into the individual ingot moulds. The conveyor is equipped with gas burners to preheat the moulds and star wheel. Water cooling is used to cool the moulds by either evaporative cooling, where water is sprayed onto the backs of the ingot moulds, or by an indirect primary quench bath, where the moulds move through a bath of water. At the end of the conveyor the ingot has cooled to approx. 250°C. The contraction is enough for the ingot to release out of the mould, using gravity when the mould turns around the end head shaft sprocket, however bronze hammers are installed at the end of the machine to assist with ejecting the moulds. The conveyor is supplied with its operating control panel, electrical wiring and pipework pre-assembled at our works before dispatch.
Automated Stacking
A pneumatically operated transfer mechanism receives the aluminium ingot from the exit point of the ingot casting machine, lowering the ingot onto the chain conveyor of the stacking line. The stacking line can be arranged at right angles to the ingot casting machine or in a straight line. The ingots pass through a reject mechanism, controlled by adjustment of two sets of lasers. If the ingot is too large or too small it is rejected a high speed into a bin at the side of the conveyor. The ingot is aligned on the chain to check it is perpendicular and centralised. Immediately afterwards, the roll over mechanism can rotate the ingot through 180 degrees, as required, according to the ingot stack design. A pneumatic stop holds the ingots to form a row, which when complete, short stroke cylinders lift the ingots clear of the chain so the robot gripper can engage and lift the row. The robot has many ingot stack bundles automatically programmed specific to the end user requirement.
- Enhanced productivity
- Bespoke design options
- Moulds in cast iron
- Moulds in cast steel
- Innovative star wheel pouring design
- No dross skimming requirement on the moulds
- Decades ingot casting design development
- Ingot casting experts
- Multiple water cooling technologies
- Automated stacking options
- Automated weighing options
- Automated labelling options
- Operator and maintenance friendly
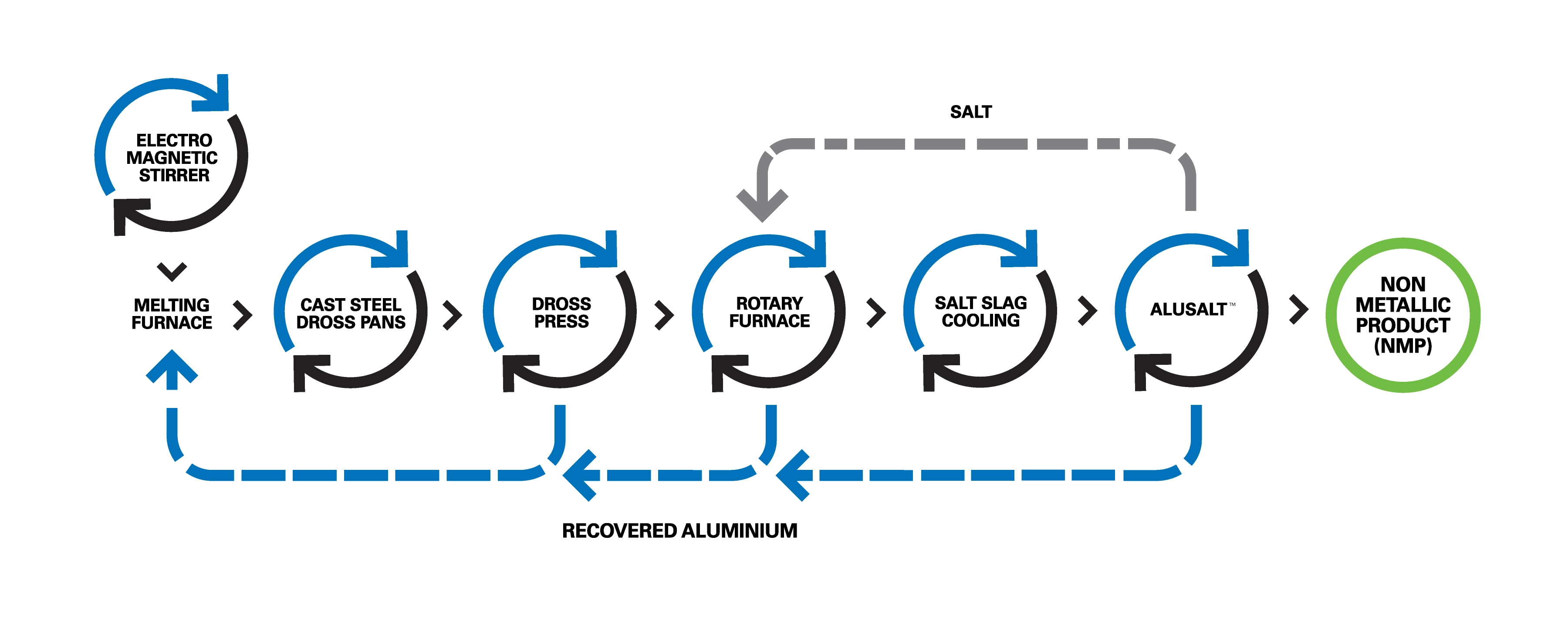
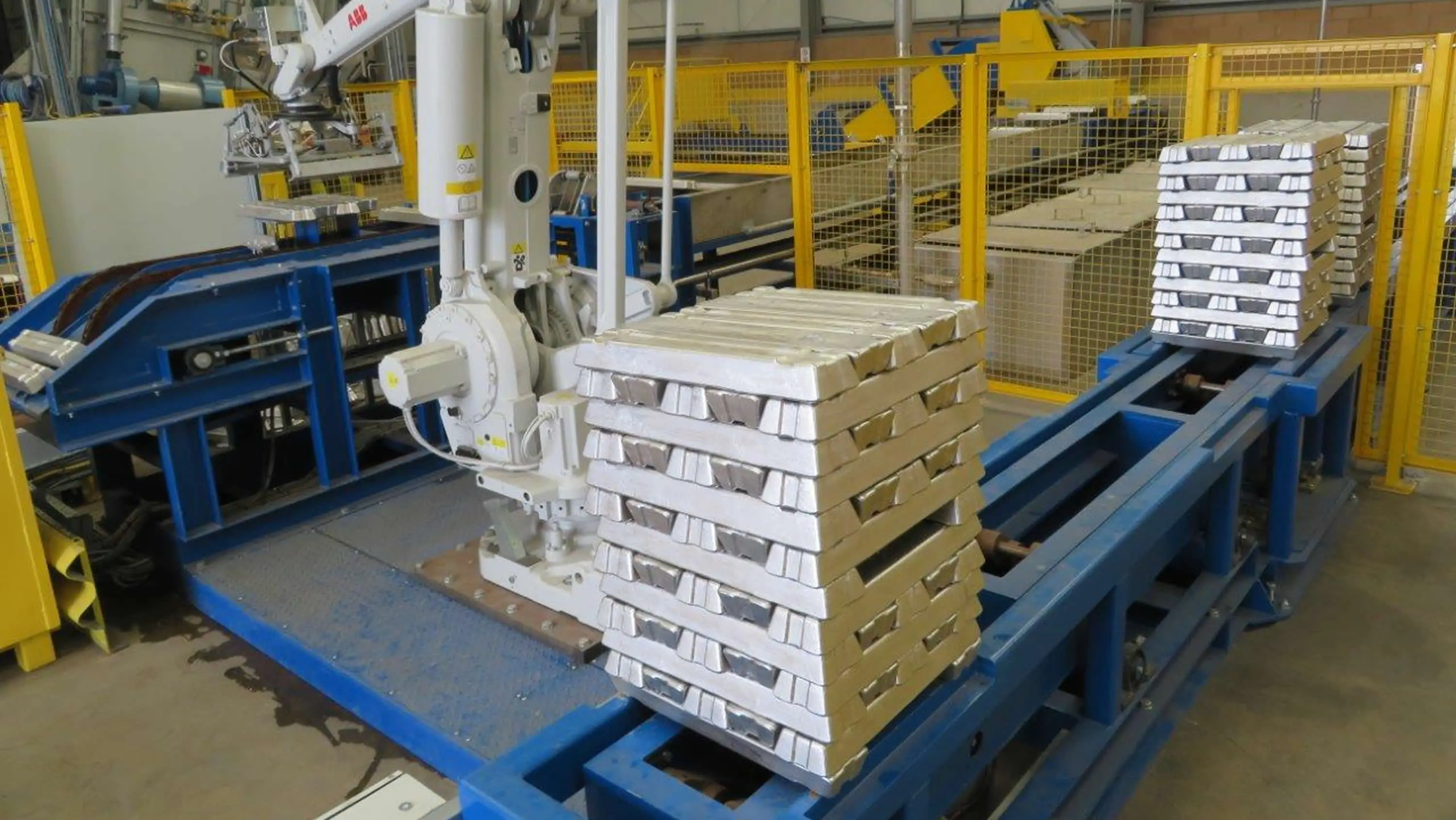
Explore new and exciting possibilities with ALTEK
Fill out the form and our sales team will reach out to start a conversation about how ALTEK can help your business save money.
For urgent enquiries, email us at altsales@harsco.com