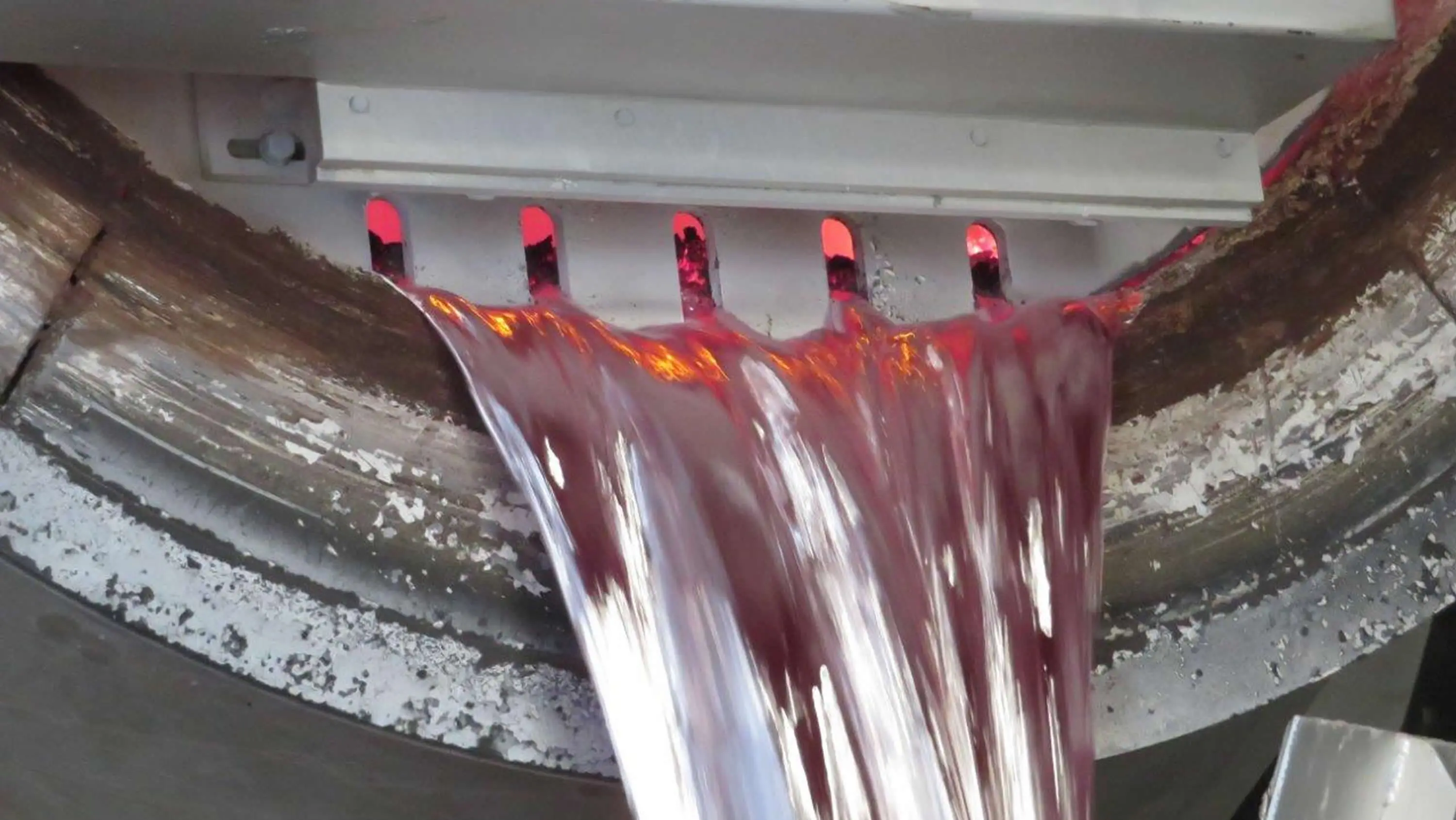
Sow Casting Lines
In sow casting, liquid aluminium is transferred from a furnace or ladle to cast steel sow moulds where the metal cools and solidifies into large aluminium blocks of typically 500kg to 1,000kg. Please visit our castings page for more information on cast steel sow mould models.
For the casting system itself, Altek offer a wide range of designs to suit the requirements of the cast house or casting operation:
Banjo Launder:
The banjo launder consists of a refractory lined launder of several metres on a pivot station, mounted on wheeled frame to allow for an operator to move the launder into position over sows. The sows are positioned in an arc and the launder is manually moved over each sow. We can design a single arc, or dual arc system, the dual arc has a split in the launder to allow for a more compact sow casting area with an inner and outer ring of sows.
Direct Line Casting
For a mechanised system we offer direct line sow casting options. Depending on the layout available we offer both single line, and twin-line options, the latter being a split tundish which can pour into 2x sow moulds at the same time. For this operation, empty sows are lined behind a tundish on a heavy duty fabricated casting line, which has two parallel heavy-duty conveyor chains (per line).
For our least automated system, the casting line is controlled by the operator. Using inverter speed control, the operator moves the moulds under the spout of the pouring tundish and will monitor the speed of the casting line throughout the pouring operation to ensure each mould is filled correctly. As soon as each mould is filled the tundish the motorized tundish is lifted to stop the flow, and track is moved forward, to the next mould and so on, until the furnace is empty, and the cast is finished. After casting the mould continues to move along the conveyor giving enough time to cool and solidify. Moulds are removed from the end of the casting line using a forklift truck in the same way as they are loaded once cooled.
For more complex systems Altek offer a range of additions to increase the level of automation, using laser level sensors linked to automated movement, robotic dross skimming, vacuum sow extraction, marking, weighing and labelling options.
Carousel / Continuous Casting
Altek also offer continuous casting systems with a range of mechanisation depending on the customer’s metal supply capacity, production rates and automation requirements. We also supply the feeding crucibles and tilting crucible pouring stations complete with heating and mixing technologies should this be required.
Molten aluminium from furnaces, or electrolysis cells, is transferred to a crucible tilting station and poured directly into sow moulds. We have options for 2x tilting stations directed into a single tundish to allow for a fully continuous casting operation. Our automated pouring and tundish system will fill the pre-heated sows to the correct level, before the sows positioned on interlinked transfer cars will index along the conveyor. Our system utilises novel poring techniques to minimise dross generation, however a dross skimming robot is still required for quality control.
The conveyor has a transfer car system between the casting and return conveyor sections, minimising ‘dead-space’ often seen in typical carousel designs. After the sows have solidified, a vacuum demoulding system transfers the sow to other stations. Depending on our customers requirements, this can be for weighing, marking, storing and stacking. The sow moulds will then return back to the casting conveyor where coating and pre-heating (if necessary) operations occur before aluminium is once again cast.
- Enhanced productivity
- Bespoke design options
- Manual to fully automated continuous casting options
- Bespoke and standard cast steel sow moulds
- Reduced dross generation pouring techniques
- Crucibles and crucible tilting stations
- Automated pouring options
- Automated stacking options
- Automated weighing options
- Automated labelling options
- Operator and maintenance friendly
Explore new and exciting possibilities with ALTEK
Fill out the form and our sales team will reach out to start a conversation about how ALTEK can help your business save money.
For urgent enquiries, email us at altsales@harsco.com