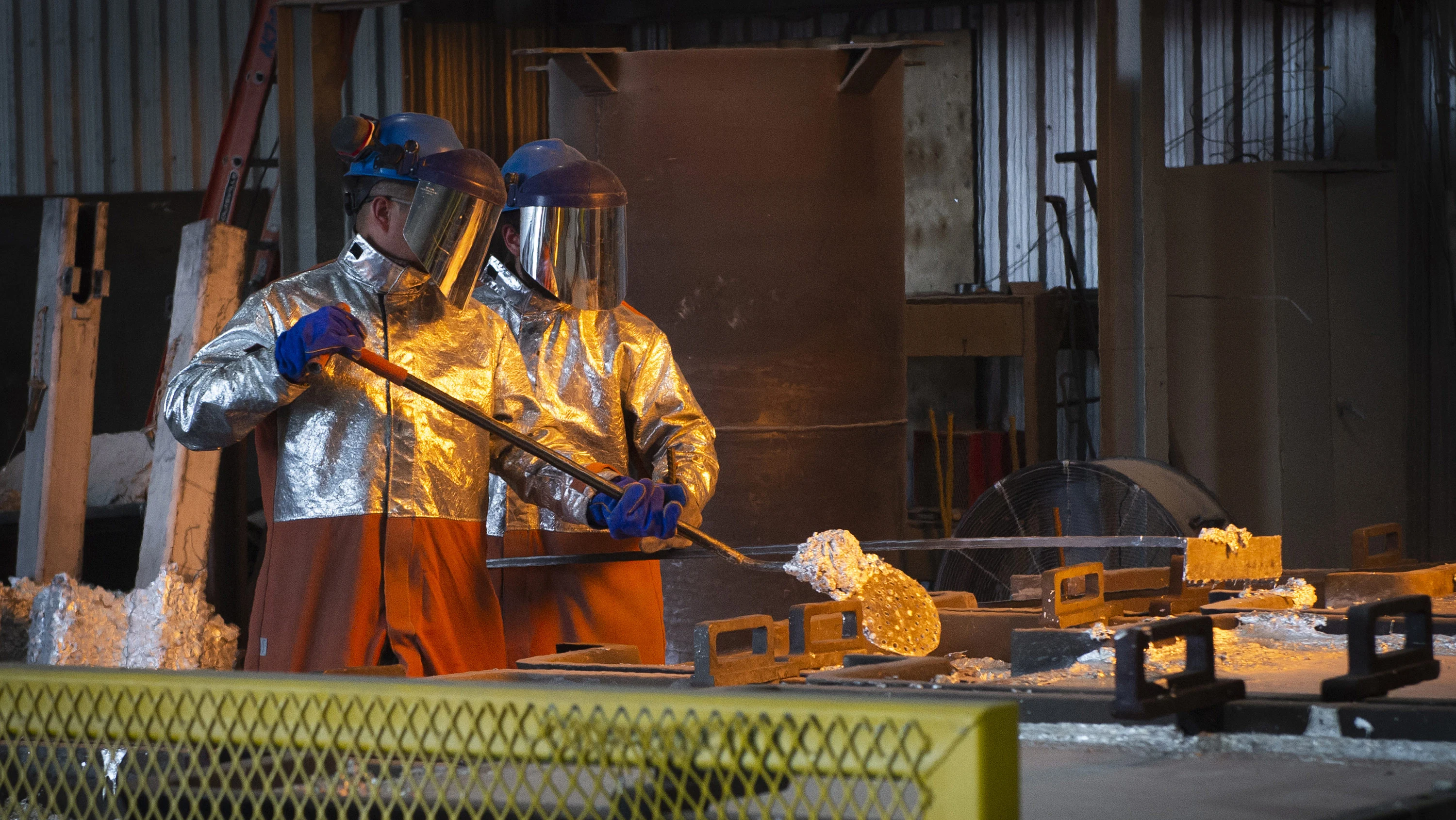
Our Latest Technology Generating Maximum Aluminium Recovery
Primary Smelters are often constrained with how to handle their dross and their overall dross management. Often located in remote regions with strict environmental permits to adhere to, smelters produce a wide variety of dross types such as; pot bottoms, furnace dross, crucible bottoms, under pot splashes, carousel dross, crucible cleaning residue which makes in-house recycling difficult.
TRFs with salt flux attain the highest yield for dross recycling, however this is undesirable for smelters who do not wish to use salt and do not wish to generate salt slag. Other salt free dross recycling technologies achieve lower yields and will still produce a by-product that needs to be removed from site. Altek now have the solution.
RAME™ is a process specifically designed for primary smelters, achieving excellent yields higher than TRF with salt flux operations, is a salt free process, and has the flexibility to process all dross types. Developed by Lefebvre, the unique feature with this process above all others is that the 100% of the output dross residues from the process are reinserted into the electrolysis cells.
This is a proven process operational for over 4 years at an Alcoa smelter processing over 17 different dross alloys, and it allows other smelters the opportunity to maximise their dross value for the first time, conserve aluminium units to reduce their carbon footprint, and boast a truly circular economy process for their dross management.
- Salt free
- Maximises aluminium recovery
- Liquid aluminium return potential
- Economical at low dross generation
- Truly zero-waste
- No GHGs used in the RAME™ technology
- No transportation off-site required
- Independence from third party processors
Explore new and exciting possibilities with ALTEK
Fill out the form and our sales team will reach out to start a conversation about how ALTEK can help your business save money.
For urgent enquiries, email us at altsales@harsco.com